Insights
Selection and Challenges of Asset Management System - Part One
2024-10-17 17:16:04
Selection and Challenges of Asset Management System - Part One
In response to the ESG trend, enterprises are actively promoting energy-saving and carbon reduction management, especially in the restructuring of global supply chain. While considering energy-saving, are enterprises also facing challenges in managing assets effectively? With the rise of Industry 4.0, the management mindset under the demographic dividend of the past few years may also need to accelerate digitization. In addition to implementing Manufacturing Execution System (MES), how should the corresponding asset management system be selected? Is it just to digitize asset management-related operations (inspection, maintenance, repair), or can it effectively improve asset availability, reduce unplanned downtime, and even improve asset utilization value through data analysis? Research indicates that asset maintenance costs can account for anywhere from 0.5% to 25% of enterprise revenue [1]. The choice of digitized system management will seriously affect the enterprise's operating performance and profitability.
Importance of the System | |||
What are the benefits of investing in an asset management system? Especially in the manufacturing industry, where MES systems have been implemented, and some have even implemented digitalized asset inspection apps, shouldn't these measures and system implementations be enough? I believe the answer should depend on the enterprise. They can examine whether there are fewer unplanned downtime and maintenance costs compared to the past after the implementation. Is the overall maintenance cycle shorter? Has the shipping quality and customer satisfaction improved? According to the report of the National Institute of Standards and Technology in the United States in 2020, the estimated annual loss caused by asset maintenance in the United States is nearly 193 billion US dollars. Especially the maintenance costs accounts for 29.6%, while the loss caused by unplanned downtime accounts for 9.4%, and the business loss caused by accidents reaches 51.7%, of which 16.1% is related to quality defects. Surprisingly, the loss caused by shipping delays is as high as 35.6%. The details are shown in Table 1. Many enterprises only consider the direct costs caused by maintenance and ignore the implicit losses. These are often caused by the lack of effective data analysis and management systems, or even still using Corrective Maintenance, waiting for the assets to break down before repairing, or lacking the ability to forecast maintenance spare parts, which seriously affects the overall business results of the enterprise. |
Table 1. Costs and losses spent on asset maintenance management in the United States [2] | |||
The asset management is divided into tangible and intangible, and the tangible part is further divided into Physical Asset or Fixed Asset, which are most valued by enterprises. It relates to the turnover and return ability of the overall capital investment and is also an important indicator that affects cash flow. Different industries will have relative fixed asset turnover levels, especially Asset-Intensive Industries that require higher asset management than Asset-light enterprises. Avoiding minor abnormal maintenance and management, whether it is the immediacy of maintenance operations, diagnosis of abnormal machines, spare parts management of repair operations, especially unplanned asset downtime affecting the overall operation and product shipping. The type, category, quantity, mode, value, and relevance to production of assets in different industries all significantly affect demand for the asset management system. It can be imagined that the pipeline asset maintenance required by public utilities (such as water, electricity, and oil) obviously needs higher immediacy of early warning and spare parts than transportation asset that does not immediately affect production and shipping. In semiconductor processes, asset values often exceed tens of millions US dollars. To ensure the unplanned downtime and timely repair, the early warning system and machine data analysis are more critical than in general electronic manufacturing industries. |
Function selection | |||
The functions of asset management systems also vary depending on the characteristics and requirements of different industries. Table 2 summarizes relevant research reports into 5 major industry categories, with the manufacturing industry further divided into four subcategories: consumer /chemical/ mechanical /electronics. Then provide selection recommendations for the main functions of 16 asset management systems based on industry characteristics and requirements, divided into three categories: necessary, preferable, and depending on enterprise scale. Among these functions: |
a. | Core Functions: | ||
Functions 1-4 provide the foundation for asset management data. They cover defining asset maintenance and contract management, implementing daily maintenance strategies (Age, Period, Block, Failure, Repair, and Opportunity), performing preventive maintenance, planning maintenance work orders, and managing costs and records of inspections, maintenance, repairs, and part replacements. All records are displayed in real-time via machine numbers or NFC scanning [3]. Functions 5-7 are primarily related to real-time and mobility. They involve managing and calculating the costs of spare parts required for repairs, and facilitating remote asset maintenance operations through the use of mobile devices. | |||
b. | Data-Driven Decision: | ||
In certain industries or large enterprises where asset downtime and maintenance time are critical, asset maintenance data analysis and reliability management become extremely important. This is particularly true in industries such as mechanical and electronic manufacturing, as well as public utility pipeline assets. Functions 8-10 mainly rely on Data-Driven Decision. By analyzing failure data to assess asset reliability and residual life, the unplanned downtime can be avoided through Predictive Maintenance. It is important to note that when conducting such analyses, data should not be limited to maintenance data from factories, but should also include Field Service maintenance data from suppliers to truly understand the health of assets. Predictive Analytics can effectively reduce unplanned downtime and maintenance time by predicting maintenance and component inventory needs. Even by using IoT devices to monitor asset operating conditions in real-time, feedback on key parameters such as temperature, stress, vibration, sound, leakage, and abnormal signals/codes can be provided to conduct Condition-Based Maintenance. This helps to understand individual component needs and initiate necessary maintenance operations in real-time, balancing maintenance efficiency and costs. | |||
c. | Intelligent Assistance: | ||
Certain industries require convenient tools to assist in ensuring operational safety and real-time maintenance. These tools help achieve timely maintenance and avoid safety or unexpected downtime losses and high maintenance costs. Functions 11-13 serve this purpose. Real-time monitoring of asset health information can be used to conduct maintenance monitoring and management using virtual reality or AI to identify the best maintenance scheduling. They can even provide autonomous maintenance plans (maintenance, repair, replacement) and system update suggestions to minimize overall maintenance costs and losses, establishing so-called Prescriptive Maintenance [4]. This type of function is particularly applicable in high-value asset management and cross-border asset management, where intelligent maintenance can be completed under conditions of reduced human intervention in data analysis and predictive model selection. |
Table 2, Industry Requirements for Asset Management System Functions [5,6] | |||
d. | Life Cycle Management: | ||
Asset-intensive industries, where the value of assets is often higher than the enterprise's annual turnover (Fixed asset turnover <1), not only focus on daily maintenance of asset but also need to attach importance to the investment efficiency, payback period, acquisition method, and even asset resale, update, and scrap management. This is part of asset life cycle management, such as public utilities and even electronic manufacturing and semiconductor industries. The goal of functions 14-15 is to provide comprehensive resource management for enterprises. | |||
By referring to the suggestions in Table 2, enterprises can determine the necessity of system functions based on their own industry characteristics and scale to select asset management systems. In addition to considering the functions of the system, the data interconnectivity with existing systems, costs flexibility for asset use, and the compatibility with the future business development of the enterprise are also important factors to consider when selecting a system. |
Author
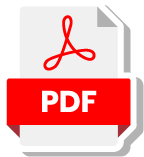
Selection and Challenges of Asset Management System - Part One.pdf
Reference
- Komonen Kai, 2002, A Cost Model of Industrial Maintenance for Profitability Analysis and Benchmarking, International Journal of Production Economics, 79, 15-31.
- Douglas Thomas, Brian Weiss, (2021), Maintenance Costs and Advanced Maintenance Techniques in Manufacturing Machinery: Survey and Analysis, International Journal of Prognostics and Health Management.
- Albert Liao, (2022),Warranty Chain Management - Digitalization and Sustainability, Springer.
- Jay lee, Jun Ni, Jaskaran Singh, Baoyang Jiang, Moslem Azamfar, Jianshe Feng, (2020), Intelligent Maintenance Systems and Predictive Manufacturing, Journal of Maufacturing Science and Engineering, Nov. Vol.142, 1100805-1.
- Kristian Steenstrup, Nicole FoustMarket, (2021), Guide for Enterprise Asset Management Software, Gartner, ID G00742599
- Juliana Beauvais, John Villali, Reid Paquin, Andrew Meyers, Kevin Permenter, (2020), IDC MarketScape: Worldwide SaaS and Cloud-Enabled Asset-Intensive EAM Applications 2020–2021 Vendor Assessment, IDC # US46261320e.
- World economic Forum, (2023), Global Lighthouse Network: Shaping the Next Chapter of the Fourth Industrial Revolution.
- World economic Forum, (2023), Global Lighthouse Network: Shaping the Next Chapter of the Fourth Industrial Revolution.