Insights
Innovation in Product Warranty Management - Part Two
2024-10-17 17:15:55
Execution | |||
After setting the warranty policy, the execution involves implementing the warranty plans for different products, including service operations, customer satisfaction, warranty process control, warranty data analysis, product reliability, warranty costs, and operational improvement review. The execution aspect mainly focuses on the product warranty plans and sets up relevant operations at four different levels: | |||
1. | Warranty claims related to satisfying customers, analyzing exceptions to avoid invalid or fraudulent warranty claims, and establishing warranty spare parts to provide real-time replacement services. | ||
2. | Warranty service-related operations aimed at improving service efficiency, including reverse logistics management, outsourcing management of service providers, and service quality monitoring. | ||
3. | Effective analysis and understanding of product and operational issues using warranty claim and service data, including warranty data acquisition and analysis, quality analysis, and product reliability. | ||
4. | The continuous improvement phase ensures that the execution of the warranty plans can achieve customer satisfaction and warranty cost control under two premises. | ||
After understanding the product reliability, theoretical analysis can be used to estimate future warranty amounts to understand potential warranty costs and operational improvement directions. This is a continuous management cycle that can effectively improve the results of the warranty plans execution, serve as a reference for the next product warranty plan, and help the enterprise systematically establish a process for warranty operations. | |||
Strategic | |||
By considering the entire product design and sustainable business model, the entire product life cycle, and the application of industry technology, the enterprise's warranty strategy and actions are established to find the most advantageous strategies for both manufacturers and customers. Of course, this must consider product attributes, warranty policies of same industry, product design, quality, and reliability while ensuring that the entire warranty service can meet product and market needs. In addition to the product warranty policy, it mainly includes the establishment of digital technology-based warranty interconnection management to understand product usage status in real-time, introduce artificial intelligence applications, automatically provide self-diagnostic and suggested solutions, and establish standard maintenance mechanisms [7]. It can be applied in warranty-related management operations and decision-making to effectively reduce warranty costs and improve customer satisfaction. The above mainly uses digital technology tools to improve the efficiency of warranty chain management. |
Furthermore, as environmental protection and sustainable development become increasingly important, establishing sustainable warranty energy is also an essential part of warranty strategy. These include product design sustainability, activities to increase material utilization and product lifespan, and establishing warranty management in the circular economy. Finally, it is essential to bear the manufacturer's warranty responsibility, whether in product or financial aspects. Moreover, establishing a systematic management platform to connect related warranty chain management activities and data can help enterprises focus on their core competitiveness, significantly improve after-sales warranty and overall product life cycle management efficiency and costs, and improve customer satisfaction and product service. | |||
Industry Application | |||
Integrating external and internal warranty strategies and execution is an inevitable challenge in innovative warranty management for enterprises. The strategic and execution aspects are interdependent in many parts, with the strategy mainly set by top executives based on industry development and market positioning. These decisions will affect the warranty plan and execution of operations, as well as the achievement of the original warranty goal. Regarding the development and design-related strategies, if new technologies are not mature or there are no suitable process control methods, the result of hasty introduction may be a high defective rate and customer complaints, which seriously affects the burden and costs of warranty services. In addition, using secondary components for low-price competition may also cause more harm, leading to inadequate durability and safety of the entire product and affecting customer rights. This is a frequently seen case that cannot be solved by warranty service alone. The warranty strategy will be adjusted according to the product strategy. It is not a one-time decision. It requires analysis, simulation, and feedback, and it needs to be inspected before the product is launched. | |||
Table 2 provides an evaluation and establishment of the necessity of individual innovative elements of warranty for common warranty service demands in manufacturing. Consumer goods manufacturing usually has shorter warranty periods and can mainly provide warranty complaint channels. However, for the electronics industry, different industry categories and scales require warranty management to consider not only complaint handling but also consideration of product defects and data analysis to effectively understand the potential risks of product quality. These factors significantly affect the proportion of warranty costs. Enterprises can gradually establish product after-sales service processes according to the industry size and development, but they need to understand the future needs of management innovation to adjust organizational structure and resources. |
Table2. Industry's demand for warranty chain management elements | |
As new products are launched and their quantities increase, and the arise of environmental awareness, products will have extended lifetimes, driving the growth of the warranty market. The management of warranty costs significantly affect the operation and profitability performance of the entire enterprise. Especially in the environment of global supply chain restructuring and the decline in hardware manufacturing profits, the planning and management of warranty operations for emerging technology products are even more important while facilitating our convenient living environment. How to manufacture high-reliability products, provide high-quality warranty services, and effectively reduce warranty costs are significant issues in industrial economic activities. In addition to warranty costs, the challenges that enterprises face in the post-sales warranty stage of the product life cycle today are: (1) increasing quality and environmental regulatory requirements; (2) real-time data needs to flow from the site to the dealer network, and then to the upstream manufacturing department and product design unit; (3) detection and correction of failure problems require long time periods; (4) there are many unregulated service and component quality in the market; (5) the lack of systematic management processes and effective feedback mechanism. All of these challenges can be overcome by innovative warranty management. | |
Innovation trends | |
Driven by industry changes and enterprise needs, complex management structures and processes require innovative solutions that can effectively enhance overall management capabilities and solve data interconnectivity issues. The rising needs of remote and cross-border management particularly in response to the flexible work-from-home operations during the pandemic have made cloud platform services a popular solution. By utilizing the platform's data interconnectivity and analysis capabilities, different levels of management needs can be effectively improved on the internal execution side. |
The application of emerging technologies can effectively replace past experience-based operations. Whether it is the introduction of artificial intelligence or monitoring through the Internet of Things to understand product operation status and provide timely repair services, all can reduce the downtime and repair quantities, effectively reducing maintenance costs. Extending product life and value are the best solutions for establishing environmental sustainability. Under the management of the entire life cycle of after-sales warranty, whether it is material selection, product refurbishment and reuse, or responsible recycling and scrap management and service provision, these are all representatives of sustainable services. It should also be the most important environmental protection issue that enterprises are concerned about besides energy conservation and carbon reduction. | |
Conclusion | |
The innovation of product warranty management is in response to industry changes and transformation, especially in the era of information explosion and pursuit of environmental sustainability. It is not only digitalization, but also the adaptation of management systems and regulations that have created the demand for new generation warranty management. The challenges faced by enterprises have also been greatly enhanced, and product design, manufacturing, and service management are indispensable. From strategy to execution, from claim management to data analysis, from warning maintenance to intelligent judgment, from extending product life to sustainable design, all of these challenges the management capabilities of enterprises. The previous section also provided suggestions on the necessity of warranty management elements based on industry characteristics and scale. Enterprises can use this to examine their current management models and find suitable platform systems to enhance their overall after-sales service capabilities. |
Author
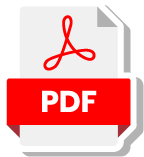
Innovation in Product Warranty Management - Part Two.pdf
Reference
- J Augustyn, (2016), Emerging Science and Technology Trends: 2016-2045 – A Synthesis of Leading Forecasts Report”, Office of the Deputy Assistant Secretary of the Army (Research & Technology)
- Mohammad Hasan, 2022, State of IoT 2022: Number of connected IoT devices growing 18% to 14.4 billion globally, IoT Analytics
- Eric Arnum, (2021),Worldwide Auto/HVAC/ Warranty Expenses, warranty week.com.
- IFRS , (2014), IFRS 15: Revenue from Contracts with Customers, Deloitte
- Wallace R. Blischke, M. Rezaul Karim, D. N. Prabhakar Murthy, (2011), Warranty Data Collection and Analysis, Springer London.
- Albert Liao, (2022),Warranty Chain Management - Digitalization and Sustainability, Springer
- Jay lee, Jun Ni, Jaskaran Singh, Baoyang Jiang, Moslem Azamfar, Jianshe Feng, (2020), Intelligent Maintenance Systems and Predictive Manufacturing, Journal of Maufacturing Science and Engineering, Nov.Vol.142, 1100805-1.